L’abbattitore di temperatura si è trasformato, nel giro di pochi anni, da semplice attrezzatura professionale a protagonista silenzioso di cucine domestiche e ristoranti stellati. Dietro il suo aspetto innocuo si nasconde una tecnologia sorprendente che, a suon di freddo rapidissimo, è in grado di cambiare per sempre il modo in cui concepiamo la conservazione, la sicurezza e la qualità degli alimenti.
Come nasce l’idea dell’abbattimento rapido
Quando si parla di abbattitori, si fa riferimento a macchine capaci di portare, in tempi brevissimi, il cuore di un alimento da temperature positive fino a valori prossimi allo zero o addirittura sottozero. L’ispirazione arriva dall’industria farmaceutica e dal settore della ricerca, dove la crioconservazione di cellule e farmaci è routine. Trasferire questo principio al mondo del cibo ha richiesto sfide ingegneristiche non banali: un flusso d’aria ultra fredda che non bruci la materia, un sistema di controllo elettronico che calibri ogni grado e un circuito refrigerante in grado di gestire l’onda gelida.
Nel corso degli anni si sono susseguite innovazioni: dall’utilizzo di gas naturali come l’anidride carbonica alle versioni a compressione più compatte per il mercato domestico. Ciò che prima era appannaggio esclusivo di chef e grandi industrie alimentari, oggi è alla portata di chiunque desideri elevare la propria cucina, ridurre gli sprechi e mettere al riparo la salute della famiglia.
Tecnologia e funzionamento oltre il cuore freddo
L’abbattitore si basa su un principio semplice ma efficacissimo: ridurre la temperatura interna di un alimento in un arco di tempo estremamente breve, mediamente tra i 90 minuti e le due ore, a seconda del volume e della conformazione. Rispetto ai normali congelatori domestici, dove la temperatura cala gradualmente con il rischio di creare cristalli di ghiaccio grossolani che danneggiano le cellule, l’abbattitore garantisce una cristallizzazione rapida e uniforme.
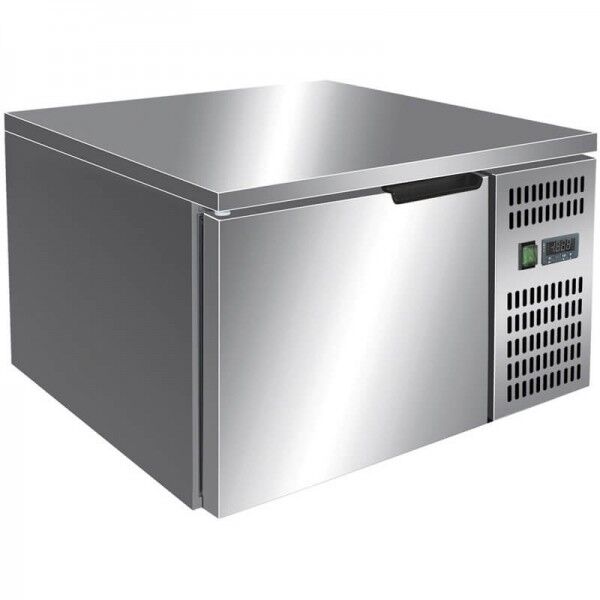
Il segreto sta nella stratificazione dell’aria refrigerata e nella gestione intelligente del flusso. Porte interne trasparenti permettono di monitorare ogni singolo ripiano, mentre display touch e sonde termiche tengono sotto controllo l’andamento del processo. Alcuni modelli di ultima generazione integrano funzioni di sbrinamento e sanificazione automatica, riducendo al minimo la manutenzione e preservando igiene e durata.
Sicurezza alimentare e qualità garantita
È nella catena del freddo che spesso si annidano insidie invisibili: proliferazione batterica, ossidazione dei grassi e perdita di nutrienti. Grazie all’abbattimento rapido, il rischio di contaminazione si riduce drasticamente. L’appassimento delle carni, il rilascio di liquidi e il deterioramento delle vitamine si arrestano come per magia, come se il tempo venisse congelato.
Questo vuol dire non solo cibo più sicuro, ma anche pietanze che, una volta riportate a temperatura di consumo, conservino aroma, consistenza e gusto quasi intatti. Che si tratti di un filetto pregiato, di un soffice pan brioche o di un dessert delicato, l’effetto finale sorprende sempre per freschezza e delicatezza, talvolta superiore anche rispetto a preparazioni appena sfornate.
Una svolta sostenibile per la cucina di domani
L’attenzione all’ambiente è un tema sempre più pressante nelle nostre vite. In questo senso, l’abbattitore di temperatura gioca un ruolo chiave nel ridurre lo spreco alimentare. Congelando con metodo, è possibile stoccare porzioni perfette di frutta, verdura e pietanze avanzate, evitando di gettarle a fine settimana. In più, molte aziende stanno studiando sistemi ibridi che integrano il recupero del calore disperso per riscaldare locali o acqua sanitaria, trasformando così un elettrodomestico a forte consumo in un alleato di efficienza energetica.
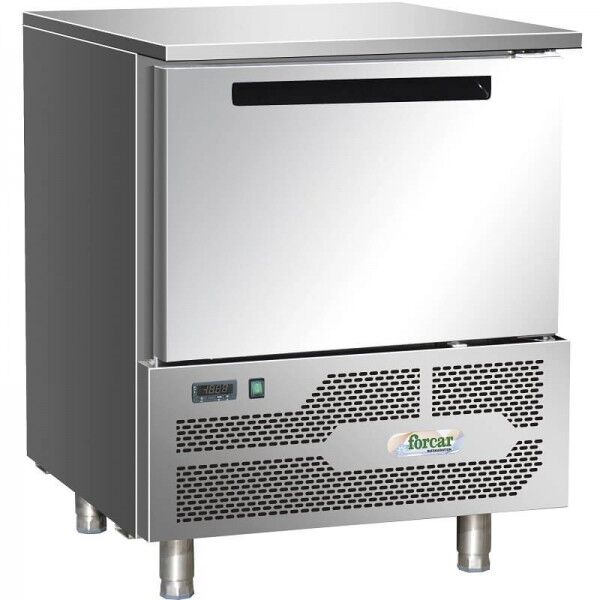
Nel settore della ristorazione, la programmazione dei menù si fa più flessibile: piatti di alta cucina possono essere preparati in anticipo e abbattuti, poi rigenerati al momento del servizio senza perdere qualità. Questo approccio aiuta a contenere i costi, a ridurre gli sprechi e a garantire un’offerta sempre variabile e di alto livello.
Conclusioni: il gelo che scalda le nostre tavole
L’abbattitore di temperatura non è soltanto un elettrodomestico dal freddo intensissimo, ma un vero e proprio alleato di chef, famiglie e imprenditori che puntano a innovazione, sicurezza e sostenibilità. Dietro ogni “click” del display si nasconde un mondo di scienza e tecnica che rivoluziona il concetto di “fresco”, preservando sapore, valori nutrizionali e bellezza estetica degli alimenti. Se la cucina è la culla della creatività, l’abbattitore ne diventa oggi il palcoscenico ideale, pronto a stupire i palati e a scrivere nuovi capitoli nella storia del gusto